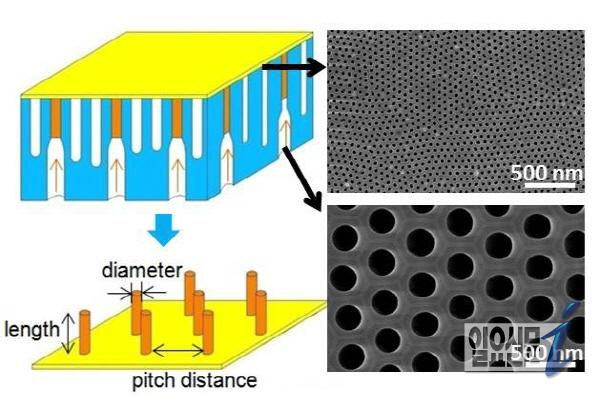
비대칭 나노플레이트 사진.
[일요신문] 국내 연구진이 나노기술을 응용해 초소형 전지의 개발과 전지기술의 혁신에 접목될 수 있는 3차원 나노집전체용 형틀기술(‘자기정렬형 알루미늄 양극산화막 제조 기술’)을 개발하는데 성공했다.
이에 따라 향후 ICT 융합형 전기전자기기용 초소형 이차전지의 개발과 실용화에 접목될 수 있을 것으로 기대된다.
한국전기연구원(원장 김호용)은 하윤철 박사팀이 물에 담근 알루미늄판에 전기를 가하는 값싼 습식 공정으로 3차원 나노집전체(集電體), 즉 나노미터급의 미세 기둥을 제조할 수 있는 알루미늄 양극산화막의 제조 공정을 세계 최초로 개발했다고 26일 밝혔다.
지난 1991년 일본 소니의 소형 리튬이온전지 상용화 이후 전 세계 유수 기업 및 대학, 연구소들은 한번 충전으로 더 오래 쓸 수 있고 충전과 방전을 수년간 거듭해도 성능이 떨어지지 않는 배터리 개발을 위해 다각적인 노력을 기울였지만 그 산업적 성과는 미미한 실정이었다.
또, 최근 급격히 증가하고 있는 초소형, 중대형 및 초대형 전지의 산업적 수요를 충족시킬 수 있는 기술개발도 이뤄지지 못하고 있다.
초소형 전지의 경우, 여러 가지 전지재료를 머리카락 굵기의 100분의 1 두께로 층층이 쌓아올린 박막전지의 형태가 오랫동안 연구돼 왔지만 단위면적당 에너지밀도가 매우 낮아 실용화에 이르지 못하고 있었다.
이를 해결하기 위해 전지의 (+)극이나 (-)극에서 전기를 모으는 집전체 구조를 평판이 아닌 나노기둥, 나노벌집 등 다양한 형태의 3차원 형상으로 만드는 기술이 연구되고 있었으나, 대부분 비싼 건식공정을 쓴다는 점이 산업화의 한계가 돼 왔다.
그 대안으로 제시되는 알루미늄 양극산화 기술은 연탄처럼 구멍이 뚫린 나노구조를 만드는 것으로, 그 전압의 크기에 나노 구멍간의 간격이 결정되므로 기존의 방법으로는 빽빽한 나노기둥들만 제조할 수 있었다.
이러한 구조는 집전체인 나노기둥들 사이에 전지재료를 넣을 공간이 없다는 점과 이 형틀을 머리카락의 반지름 정도 두께만큼 만드는데 하루가 꼬박 걸리는 문제가 있었다.
연구팀은 지난 2011년 개발해 기술 이전한 ‘고전계 양극산화 장치’와 용액에 알루미늄 표면처리를 위한 약간의 첨가제를 섞는 방식으로 기존 형틀 제조의 한계전압으로 알려진 150V 이상의 전압에서도 전압의 크기에 따라 구멍이 규칙적으로 배열된 형틀을 제조할 수 있음을 세계 최초로 규명하고 관련 논문을 나노패터닝 분야 세계적인 과학저널인 나노테크놀러지(Nanotechnology)에 최근 게재했다.
이와 함께 저전압에서 나노구멍을 형성하고 고전압으로 나노구멍의 간격을 제어하는 방식으로 나노기둥이 듬성듬성 자라게 할 수 있는 형틀을 시연해 보이는데 성공했다.
이번 개발로 연구팀은 차세대 초소형·고에너지밀도의 전지 개발을 위한 교두보를 확보할 수 있게 됐다.
특히 이러한 기술이 전량 수입에 의존하는 상용 알루미나 멤브레인(AnodiscTM)의 사양인 47 mm, 두께 60 um급 산화막을 고속으로 제조하는 데 활용될 수 있어 상업적으로 실용성이 커 보인다.
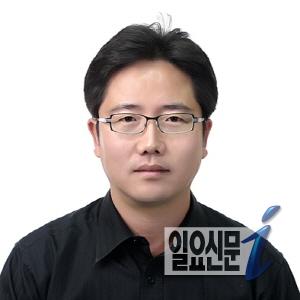
한편, 이번 연구에는 연구팀의 특허기술을 이전 받은 나노분야 연구장비 전문 제조업체인 ㈜테라리더의 고전계 양극산화장치가 이용됐다.
㈜테라리더는 이러한 기술을 통해 기술혁신형 중소기업 인증을 획득한 기업이다.
현재 ㈜테라리더는 0~300 V 범위에서 다양한 금속의 양극산화 현상을 연구할 수 있는 자동제어형 양극산화 시스템을 상품화해 기업과 연구소 및 대학에 납품하고 있다.
추가적으로 전기전자 및 에너지 소자용 나노템플레이트의 제조사업도 검토 중이다.
하용성 기자 ilyo11@ilyo.co.kr